welcome
about action
action in 2021
SUSTAINABILITY
PEOPLE
planet
product
partnership
future
governance
appendices

Waste management

Energy usage and emissions
CONTENT PLANET PILLAR
Every day Action

As part of our efforts to reduce energy consumption in our stores, we have started to replace all existing fluorescent lighting with LED lights, which use 50% less electricity. With an average of 250 lights per store, the energy and cost savings really add up. By the end of 2021, over 1,100 of our stores had only LED lights. The lights of all remaining stores will be replaced in 2022.
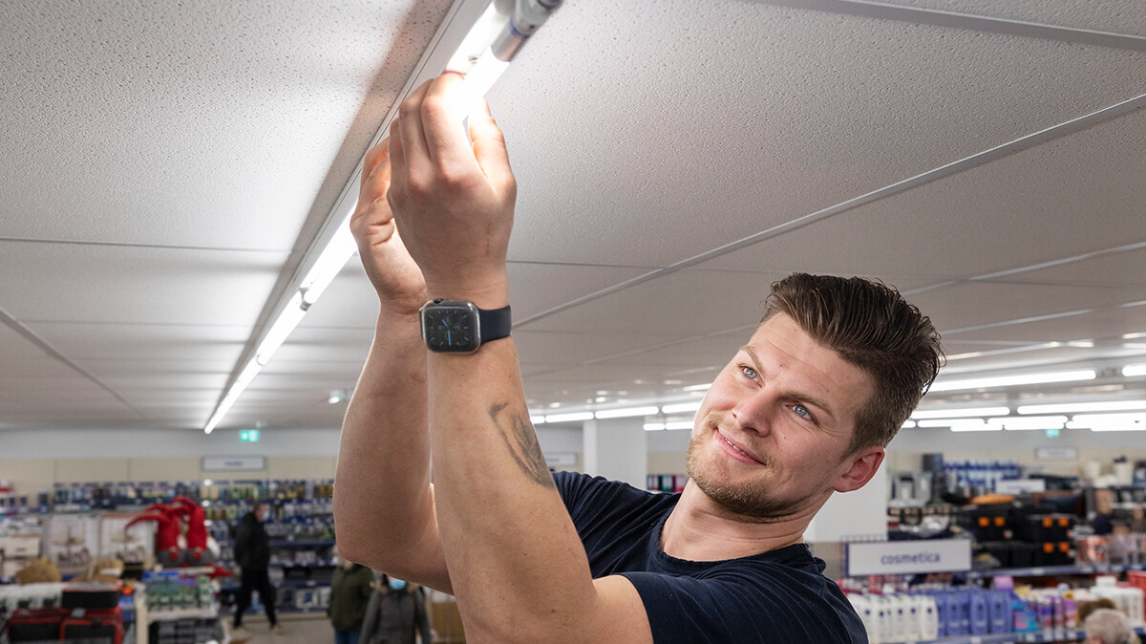
As a growing retailer with activities involving (transport to) stores, distribution centres and offices, we are aware that we not only consume natural resources but also produce waste and emissions that impact the environment, people and future generations. We therefore strive to reduce the emissions from our own operations by 50% by 2030 (Scope 1 and 2, versus the 2020 baseline).
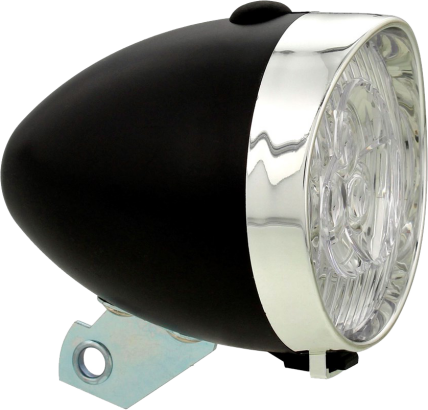
- More than 50% of our stores are now fitted with energy efficient LED lights
- Our new distribution centres achieved Very Good (Bratislava) and Excellent (Bierún) BREEAM status
- Solar panels installed on our largest distribution centre (Zwaagdijk) which will deliver 85% of its energy needs
- Detailed baseline of our Scope 1 and 2 carbon emissions
Energy use in our stores, distribution centres and outbound logistics (like transport of products from distribution centres to stores) emit greenhouse gases. These direct emissions (Scope 1) and indirect emissions from purchased electricity (Scope 2) are at the heart of our energy and emission reduction strategy. Our ambition is to reduce our Scope 1 and 2 emissions by 50% by 2030 (versus the 2020 baseline). Starting in 2022, we will also take steps to map Scope 3 emissions (not directly under our control) related to our inbound logistics.
Measures to reduce energy and emissions need to be data driven. In 2020, we investigated several potential suppliers and alternative energy management systems. We selected a system that offered the best value for money. The rollout in the Netherlands in 2021 confirmed that this energy management system matches our needs in terms of support, functionality and scalability. This allowed us to establish our emissions baseline in 2021 and monitor progress. It however needs to be considered that during 2020, a large part of our store base was impacted by, or even closed due to, COVID-19 related restrictions.
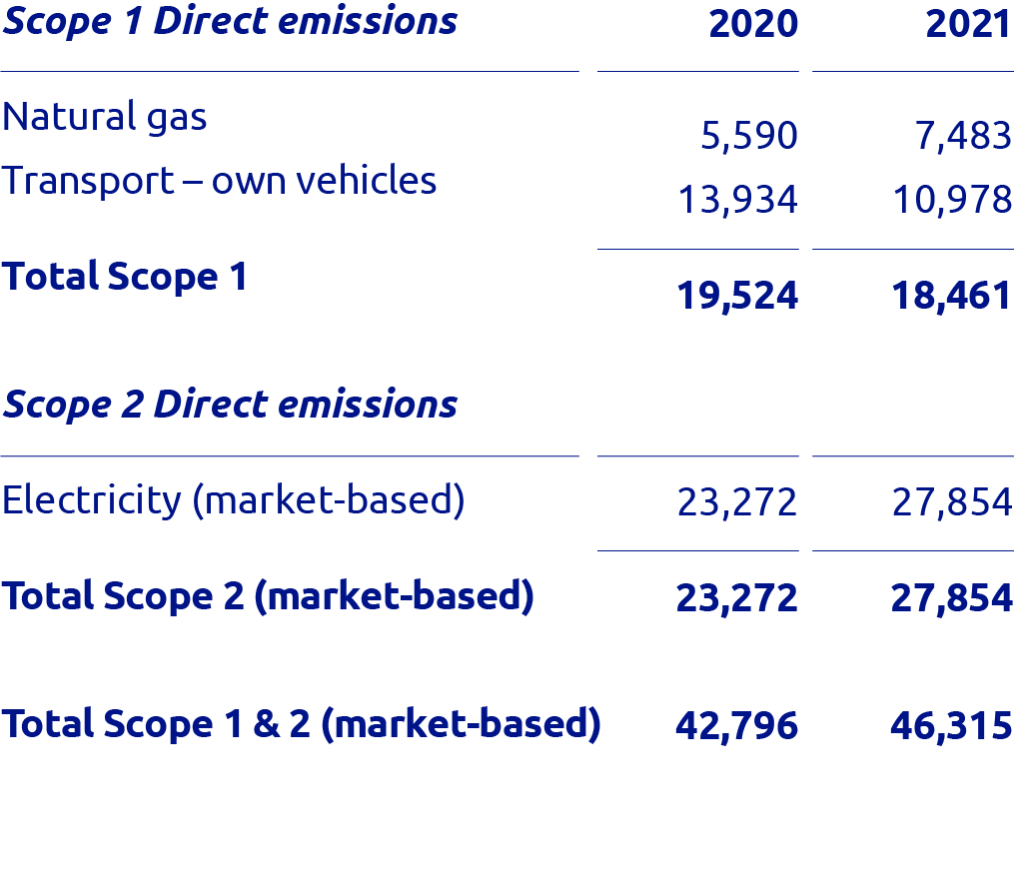
In addition to reducing our energy consumption, we will also increasingly use renewable energy in our stores, starting in 2022 in the Netherlands, Belgium, Germany, France and Luxembourg. By 2023, all electricity used in our stores, offices and distribution centres will come from renewable sources.
Our disclosures on greenhouse gas (GHG) emissions are partially aligned to the Task Force on Climate-related Financial Disclosures (TCFD) framework.
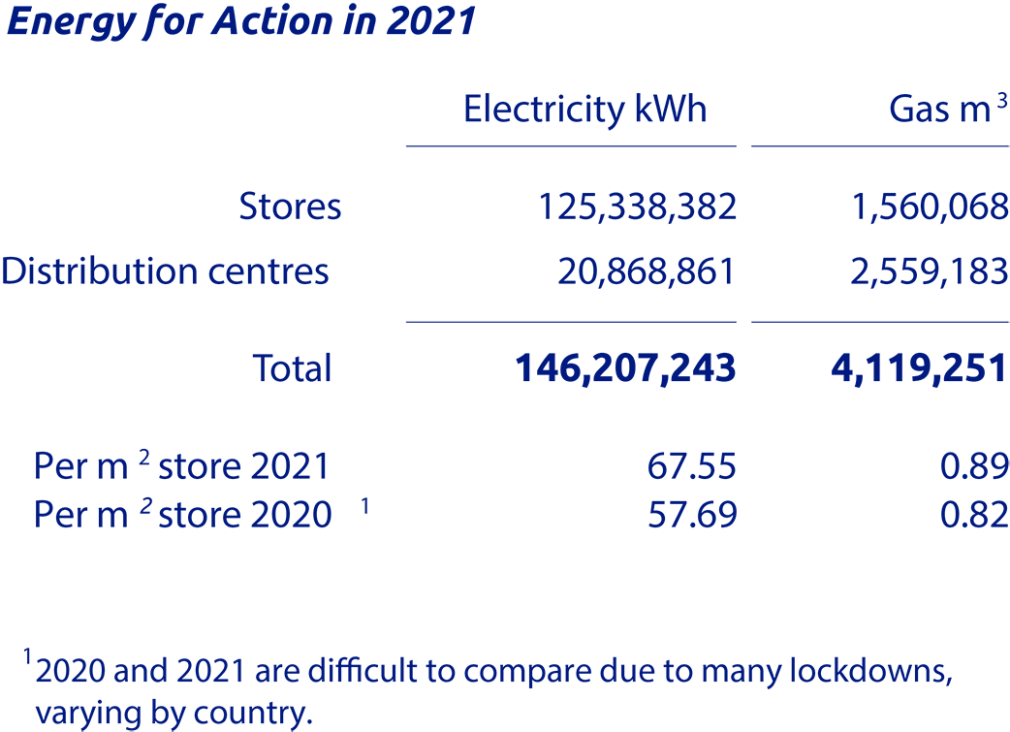
- Energy consumption reduction by 15% per m2 by 2024 (versus 2020);
- Gas connections removed from all stores by the end of 2024;
- Renewable energy used in all stores by the end of 2022.
To reduce energy consumption in our stores, we have implemented a digital electricity management system. By the end of 2021, 50% of our stores had digital meters, connected to an energy management portal. This allows us to benchmark the performance of our stores and to identify irregular consumption patterns. In the course of 2022, all our stores will be connected to the portal.
As our stores significantly contribute to our overall energy consumption, we have accelerated our emission reduction efforts in our stores to achieve:
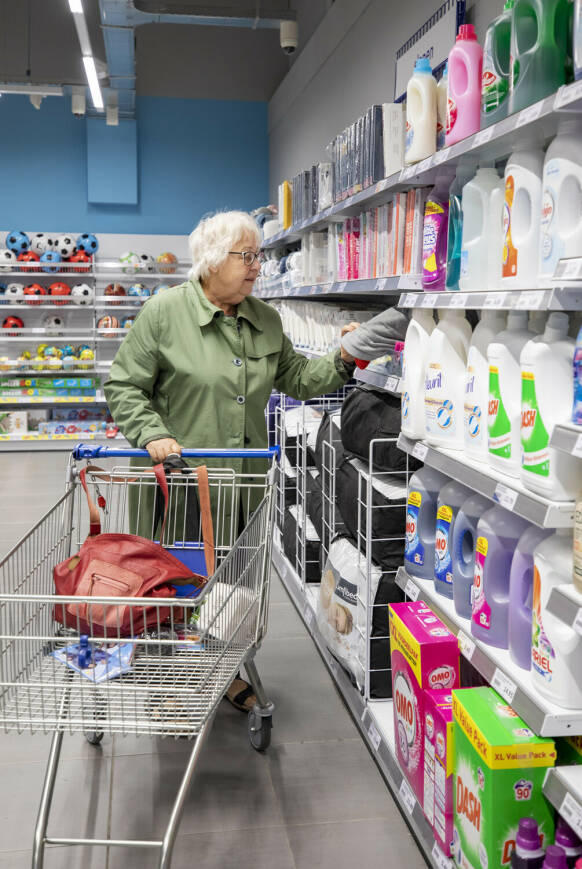
- Energy consumption reduction;
- Doubling our own energy generation capacity by 2024 (versus 2020) by installing solar panels;
- Renewable energy used in all distribution centres by the end of 2022.
We build our distribution centres based on the latest technological construction requirements for ecological and environmentally friendly operations, in alignment with BREEAM standards, an international rating system for sustainable building constructions (or comparable certification standards). The distribution centres completed in 2021 have a Very Good (Bratislava, Slovakia) and an Excellent (Bierún, Poland) BREEAM rating. For future distribution centres, BREEAM Excellent certification will become our standard.
Key steps on the way to halving our carbon footprint by 2030 for our distribution centres are:
Transport is a substantial contributor to greenhouse gas emissions globally. The sector is transforming, partly due to the pressure of legislative initiatives, such as the implementation of emission-free zones. For our outbound logistics (the transport of products from distribution centres to stores), diesel will be phased out over time. We consider electric transport as the long-term solution for both short- and long-range transportation.
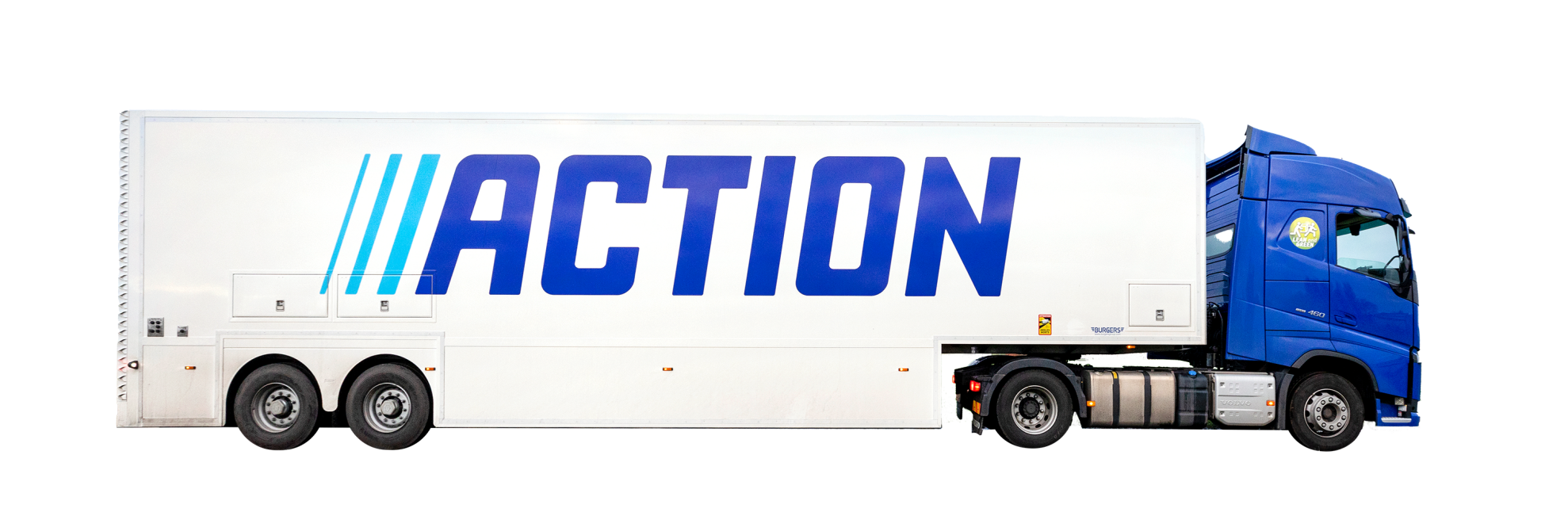
We are continuously working to reduce the average number of kilometres driven. In 2021, the average distance between a store and distribution centre was 189 km, 4.5% lower than in 2020. We will continue to accomplish shorter average distances by further expanding our logistics network with new distribution centres or hubs every year.
Our outbound logistics are operated by our own fleet, as well as by third parties. We therefore report on the CO2 emissions of these two types of outbound logistics separately: the emissions of our own fleet are Scope 1, while outsourced logistics are Scope 3 emissions. The relative reduction of emission per collo in 2021 was achieved by reduced distance to the stores, improved fuel efficiency and the HVO pilot in the Netherlands.
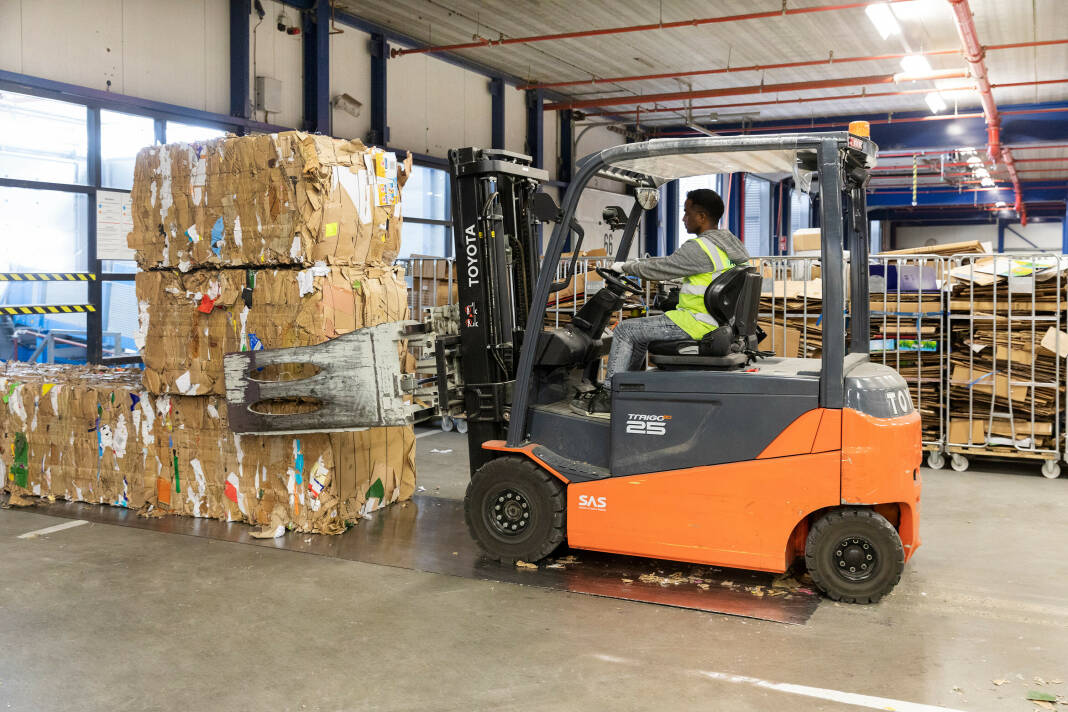
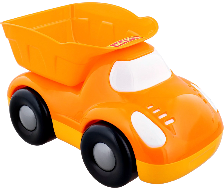
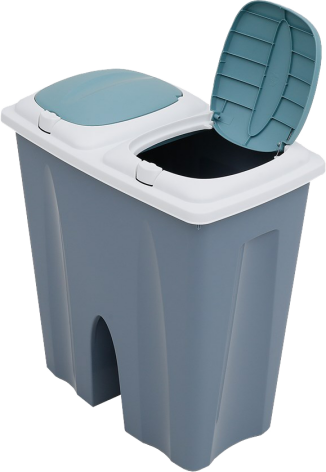
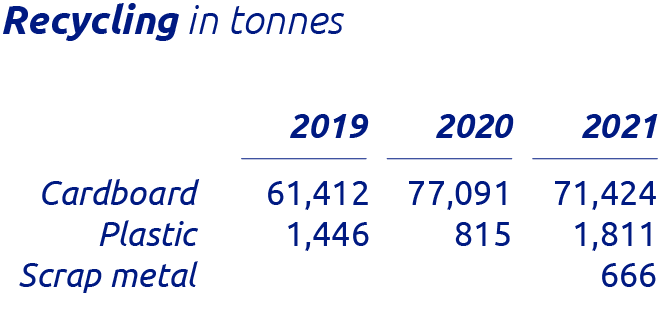
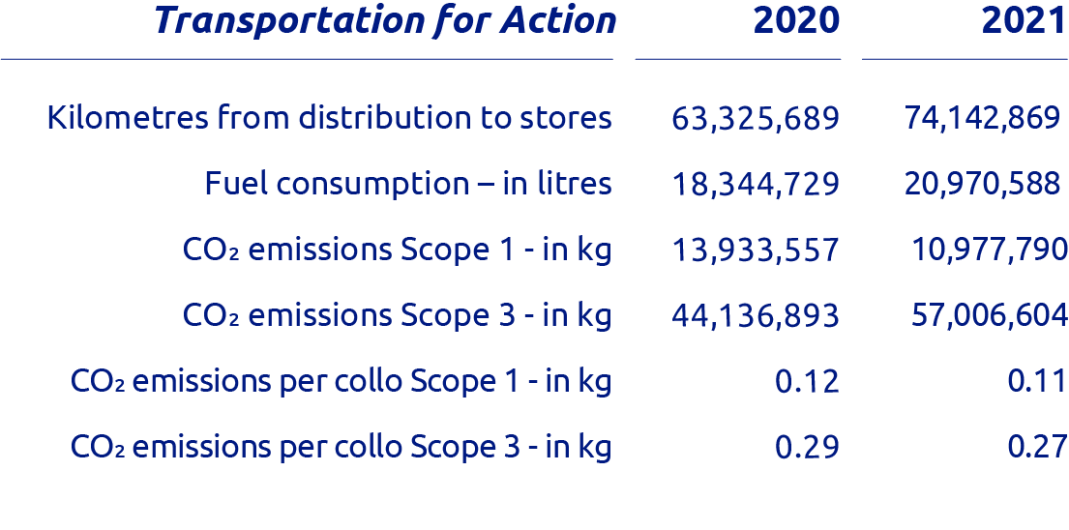
Our main waste streams are cardboard and plastic which are used for product protection during transportation. We also process damaged and returned products, primarily to avoid these products becoming waste.
Cardboard and plastic are collected in the stores and distribution centres and recycled. At our distribution centres, we compress the volume of cardboard and plastic before it is passed on to recycling facilities. By reducing the volume, we can transport these materials more efficiently, which helps minimise CO2 emissions. The compressed bales also comply with the recycling facilities’ standard way of working, so no extra handling is required.
We also prevent plastic use by only stretch wrapping the upper part of the roll containers, saving an estimated 30% in plastics compared to fully wrapping each container.
Throughout the year, when stores are refurbished, enlarged or relocated, we also demount, collect, sort and store racking for reuse or recycling. Store checkouts are refit, restyled to comply with current format standards and reused after a store refurbishment. Additionally, in collaboration with our suppliers, we also collect and reuse cleaning machines, our safes and individual components of IT systems still fit for purpose.
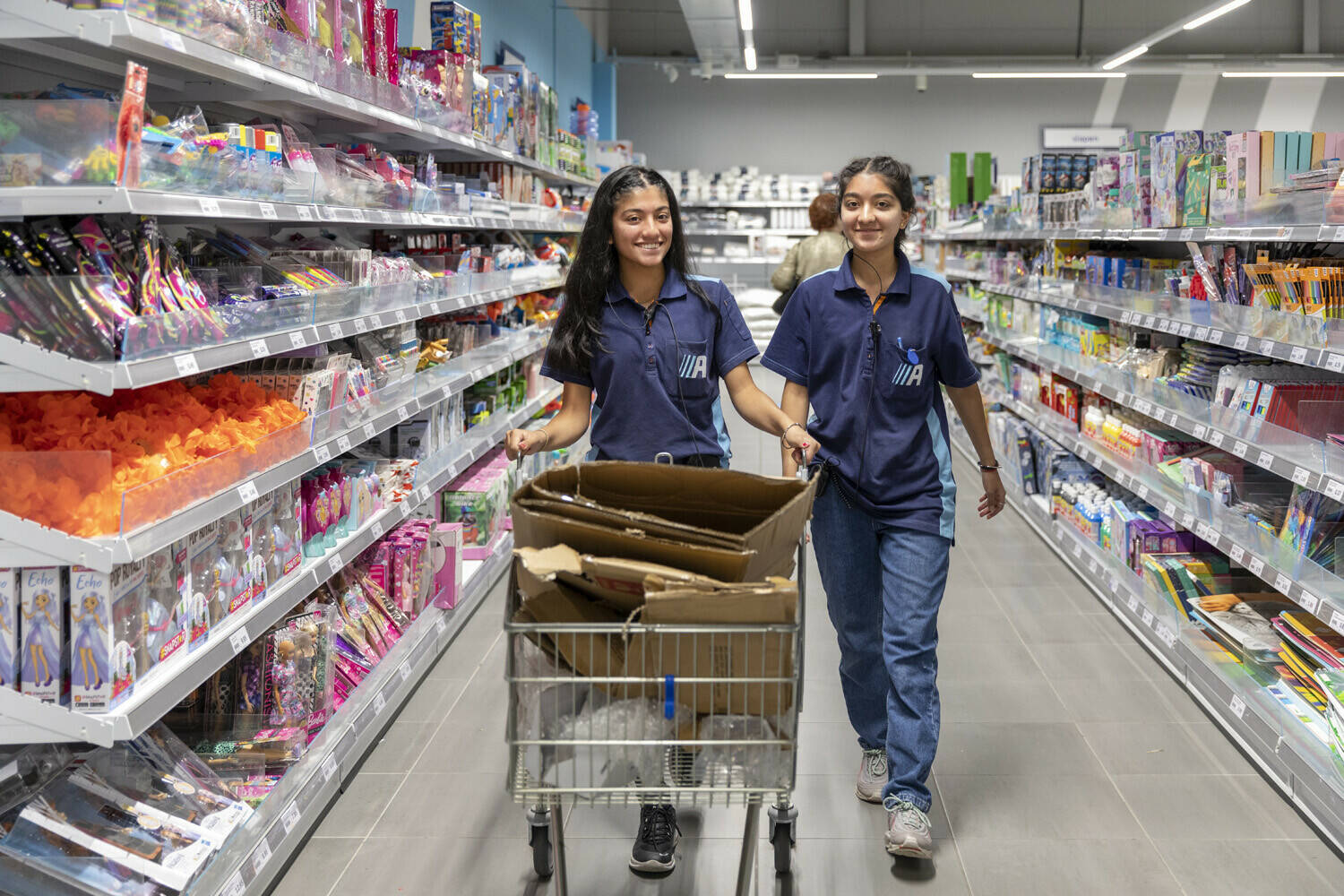
We provide our customers with an organised way to dispose of batteries, light bulbs and small electrical appliances. We do this in partnership with local partners and initiatives such as Intesia in Austria, the Czech Republic, France, Germany, Italy, Poland and Spain; GP Groot, Stichting Open and Stibat in the Netherlands and Cebat in Belgium.
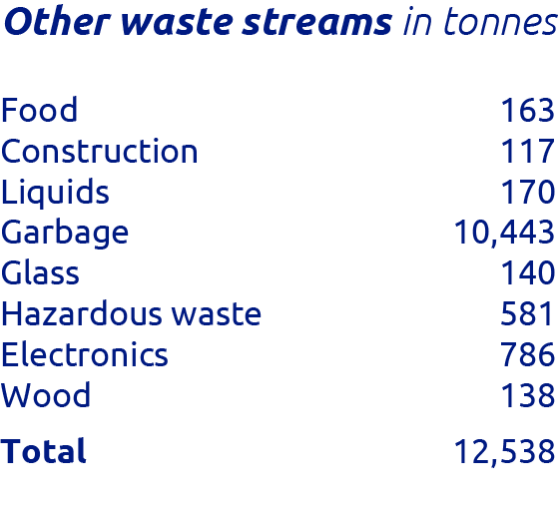
We work with several transport service providers for the execution of all inbound flows of products, sourced from our global suppliers. Although we do not control these activities and the resulting emissions, we do acknowledge that these activities are conducted for the benefit of our business.
In 2022, we will start investigating and mapping the CO2 footprint of our inbound logistics flows. Based on these insights, we will be better positioned to define priorities and ways to reduce CO2 emissions in this part of our supply chain.
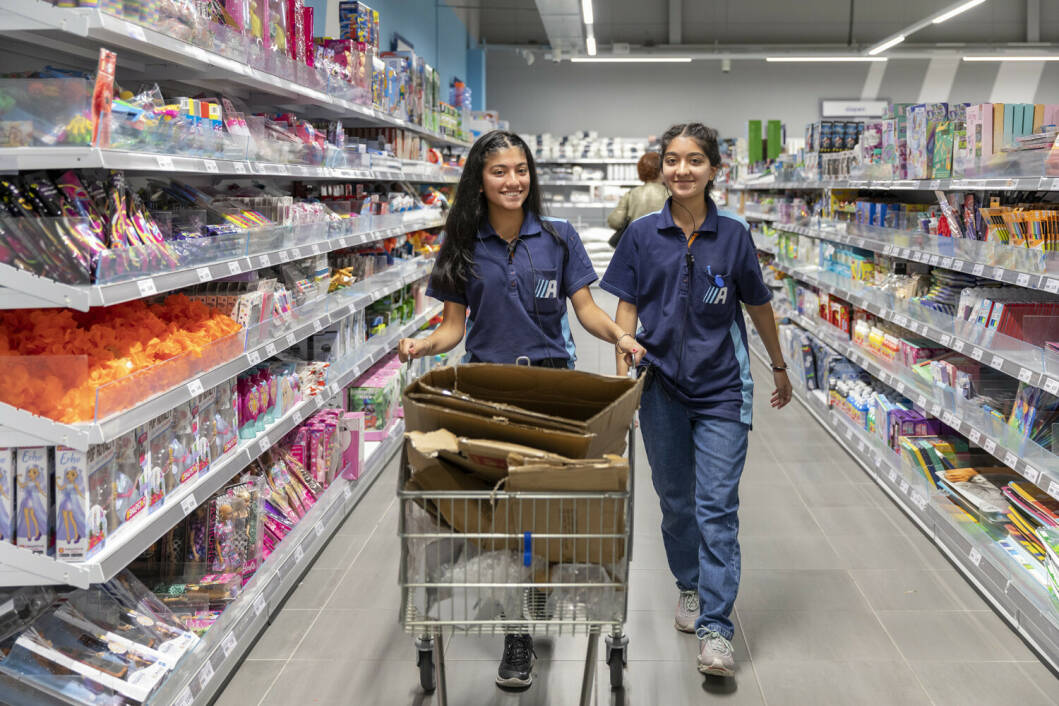
We provide our customers with an organised way to dispose of batteries, light bulbs and small electrical appliances. We do this in partnership with local partners and initiatives such as Intesia in Austria, the Czech Republic, France, Germany, Italy, Poland and Spain; GP Groot, Stichting Open and Stibat in the Netherlands and Cebat in Belgium.
Throughout the year, when stores are refurbished, enlarged or relocated, we also demount, collect, sort and store racking for reuse or recycling. Store checkouts are refit, restyled to comply with current format standards and reused after a store refurbishment. Additionally, in collaboration with our suppliers, we also collect and reuse cleaning machines, our safes and individual components of IT systems still fit for purpose.
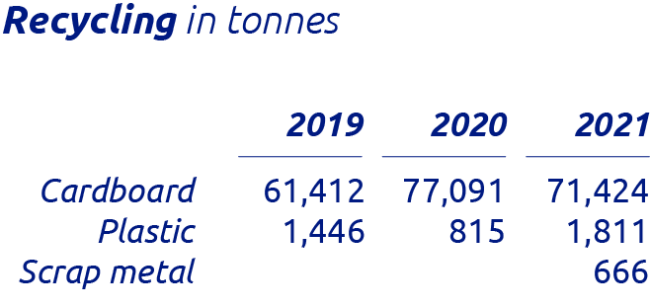
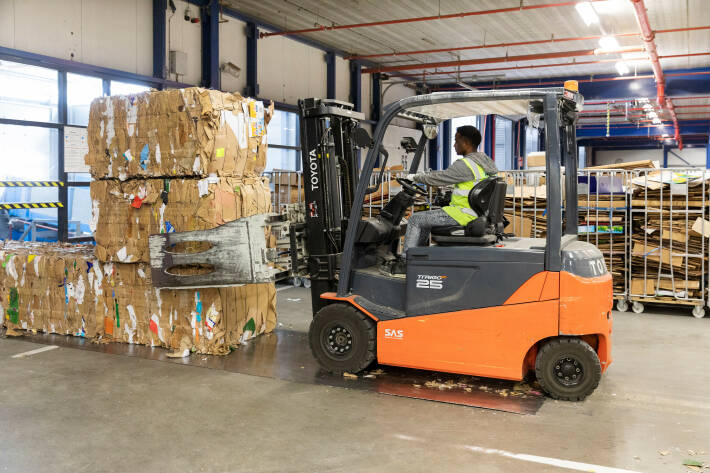
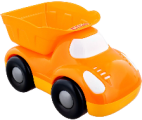
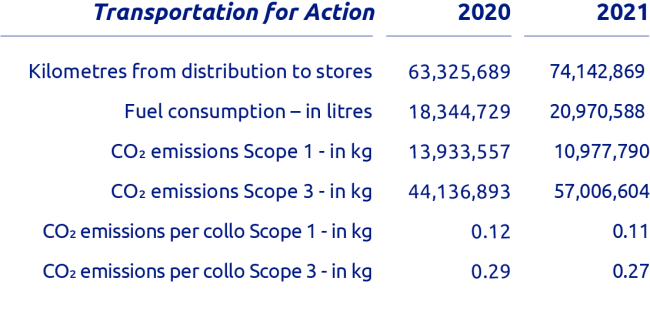
Our main waste streams are cardboard and plastic which are used for product protection during transportation. We also process damaged and returned products, primarily to avoid these products becoming waste.
Cardboard and plastic are collected in the stores and distribution centres and recycled. At our distribution centres, we compress the volume of cardboard and plastic before it is passed on to recycling facilities. By reducing the volume, we can transport these materials more efficiently, which helps minimise CO2 emissions. The compressed bales also comply with the recycling facilities’ standard way of working, so no extra handling is required.
We also prevent plastic use by only stretch wrapping the upper part of the roll containers, saving an estimated 30% in plastics compared to fully wrapping each container.
We are continuously working to reduce the average number of kilometres driven. In 2021, the average distance between a store and distribution centre was 189 km, 4.5% lower than in 2020. We will continue to accomplish shorter average distances by further expanding our logistics network with new distribution centres or hubs every year.
Our outbound logistics are operated by our own fleet, as well as by third parties. We therefore report on the CO2 emissions of these two types of outbound logistics separately: the emissions of our own fleet are Scope 1, while outsourced logistics are Scope 3 emissions. The relative reduction of emission per collo in 2021 was achieved by reduced distance to the stores, improved fuel efficiency and the HVO pilot in the Netherlands.
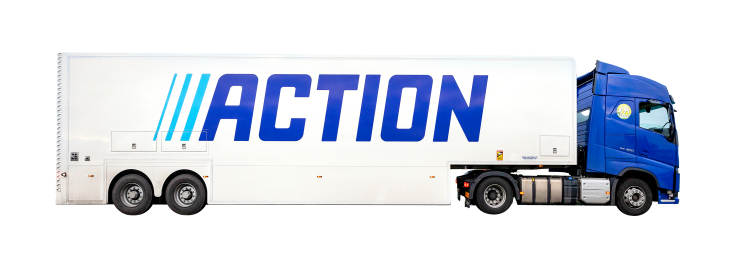
The relevant battery and hydrogen-based technologies are, however, not yet available at a sufficient scale. We are therefore considering intermediate solutions for the coming years. We have the ambition significantly reduce our carbon footprint from transport (Scope 1 and 3) by 2030 but are clearly dependent on the technological progress made. In 2021, we conducted a pilot with ten trucks driving on hydrotreated vegetable oil (HVO). This alternative fuel made of waste resources generates up to 90% lower CO2 emissions compared to diesel. In 2022, we intend to roll-out the use of HVO to a substantial part of our fleet operating from the Netherlands. We will also invest in two electric trucks to assess the possibilities and implications of the electrification of our (entire) truck fleet.
Transport is a substantial contributor to greenhouse gas emissions globally. The sector is transforming, partly due to the pressure of legislative initiatives, such as the implementation of emission-free zones. For our outbound logistics (the transport of products from distribution centres to stores), diesel will be phased out over time. We consider electric transport as the long-term solution for both short- and long-range transportation.
We run our distribution centres in an energy efficient manner: in and around the distribution centres, we use electric transport to limit CO2 emissions and reduce noise and exhaust levels on site. Our distribution centres are fitted with LED lights and light sensors, reducing energy consumption. To identify further energy saving potential, we regularly conduct energy audits and update functional specifications to include these audit findings.
In 2021, as part of our energy reduction efforts, we started to connect our distribution centres to our digital electricity management system as well. Five of the distribution centres had digital meters by the end of 2021, the remaining distribution centres will be connected in 2022.
For our distribution centres, switching from natural gas to green energy can be complex due to the technical infrastructure, legislative requirements and grid capacity. We have engaged a specialized advisory firm to guide us in this process. We aim to have specific plans in place by 2023.
We will maximize the use of solar panels in all our current and future distribution centres. In 2021, we installed solar panels on our distribution centre in Zwaagdijk (the Netherlands), which will provide 85% of its energy needs in the future. Across all distribution centres, 10% of electricity was sourced through solar panels. In early 2022, solar panels will be installed on our distribution centre in Verrières (France). In consultation with the lessors of our distribution centres, further potential for generating solar energy will be assessed.
- Energy consumption reduction;
- Doubling our own energy generation capacity by 2024 (versus 2020) by installing solar panels;
- Renewable energy used in all distribution centres by the end of 2022.
We build our distribution centres based on the latest technological construction requirements for ecological and environmentally friendly operations, in alignment with BREEAM standards, an international rating system for sustainable building constructions (or comparable certification standards). The distribution centres completed in 2021 have a Very Good (Bratislava, Slovakia) and an Excellent (Bierún, Poland) BREEAM rating. For future distribution centres, BREEAM Excellent certification will become our standard.
Key steps on the way to halving our carbon footprint by 2030 for our distribution centres are:
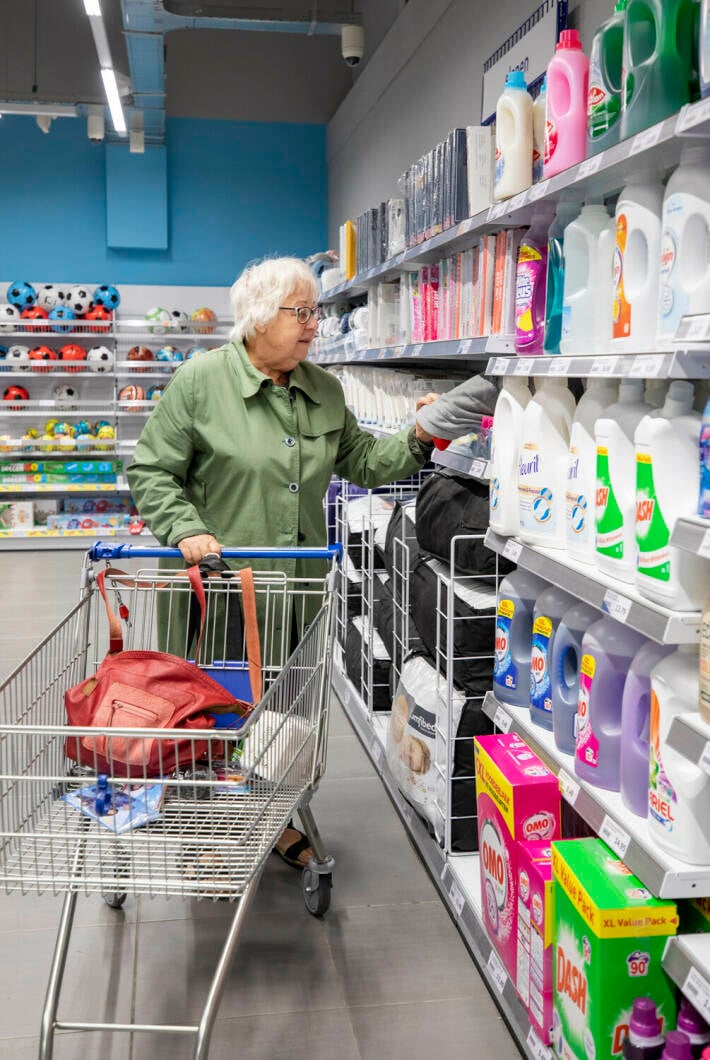
By the end of 2024, all our stores will have ceased to use natural gas. Gas connections will be replaced to enable a full switch to electricity. By the end of 2021, already 1,593 of our stores were gas-free. In 2022, another 115 stores will switch to electricity. In 48 refurbished stores, we replaced tube lighting with LEDs and installed energy-efficient heating, ventilation and air-conditioning systems (HVAC). We also reclaimed and reused refrigerant from our stores. Refrigerants are extremely potent greenhouse gases, if not treated properly. In partnership with Daikin, refrigerant gas was collected from 23 refurbished Action stores for reuse.
- Energy consumption reduction by 15% per m2 by 2024 (versus 2020);
- Gas connections removed from all stores by the end of 2024;
- Renewable energy used in all stores by the end of 2022.
To reduce energy consumption in our stores, we have implemented a digital electricity management system. By the end of 2021, 50% of our stores had digital meters, connected to an energy management portal. This allows us to benchmark the performance of our stores and to identify irregular consumption patterns. In the course of 2022, all our stores will be connected to the portal.
As our stores significantly contribute to our overall energy consumption, we have accelerated our emission reduction efforts in our stores to achieve:
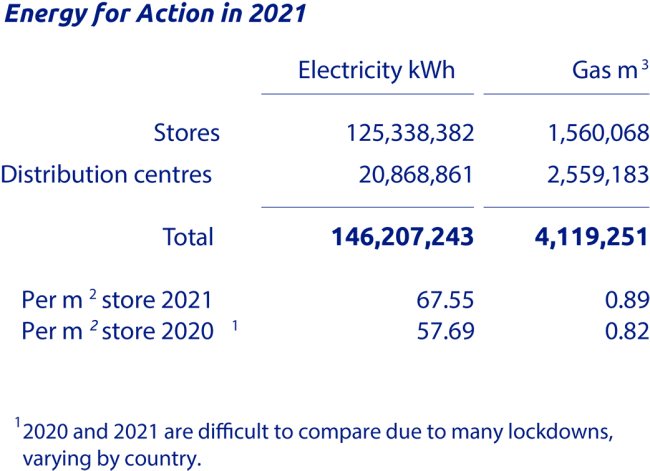
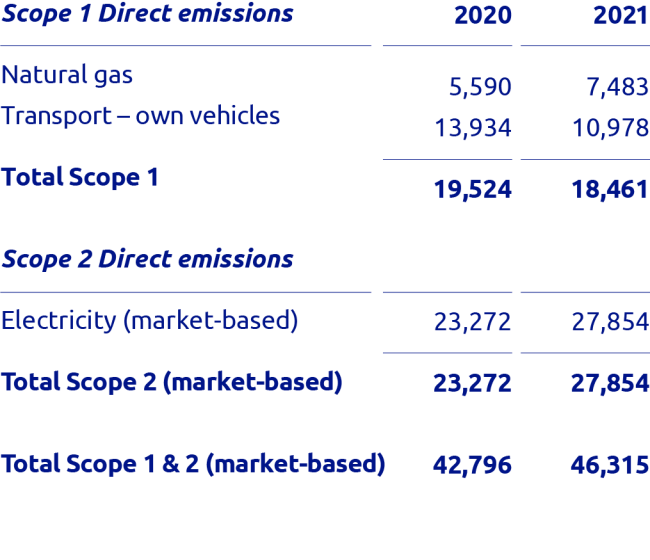
In addition to reducing our energy consumption, we will also increasingly use renewable energy in our stores, starting in 2022 in the Netherlands, Belgium, Germany, France and Luxembourg. By 2023, all electricity used in our stores, offices and distribution centres will come from renewable sources.
Our disclosures on greenhouse gas (GHG) emissions are partially aligned to the Task Force on Climate-related Financial Disclosures (TCFD) framework.
Energy use in our stores, distribution centres and outbound logistics (like transport of products from distribution centres to stores) emit greenhouse gases. These direct emissions (Scope 1) and indirect emissions from purchased electricity (Scope 2) are at the heart of our energy and emission reduction strategy. Our ambition is to reduce our Scope 1 and 2 emissions by 50% by 2030 (versus the 2020 baseline). Starting in 2022, we will also take steps to map Scope 3 emissions (not directly under our control) related to our inbound logistics.
Measures to reduce energy and emissions need to be data driven. In 2020, we investigated several potential suppliers and alternative energy management systems. We selected a system that offered the best value for money. The rollout in the Netherlands in 2021 confirmed that this energy management system matches our needs in terms of support, functionality and scalability. This allowed us to establish our emissions baseline in 2021 and monitor progress. It however needs to be considered that during 2020, a large part of our store base was impacted by, or even closed due to, COVID-19 related restrictions.
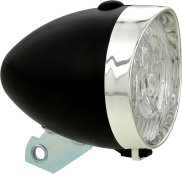
- More than 50% of our stores are now fitted with energy efficient LED lights
- Our new distribution centres achieved Very Good (Bratislava) and Excellent (Bierún) BREEAM status
- Solar panels installed on our largest distribution centre (Zwaagdijk) which will deliver 85% of its energy needs
- Detailed baseline of our Scope 1 and 2 carbon emissions

Waste management

Energy usage and emissions
CONTENT PLANET PILLAR
As a growing retailer with activities involving (transport to) stores, distribution centres and offices, we are aware that we not only consume natural resources but also produce waste and emissions that impact the environment, people and future generations. We therefore strive to reduce the emissions from our own operations by 50% by 2030 (Scope 1 and 2, versus the 2020 baseline).
As part of our efforts to reduce energy consumption in our stores, we have started to replace all existing fluorescent lighting with LED lights, which use 50% less electricity. With an average of 250 lights per store, the energy and cost savings really add up. By the end of 2021, over 1,100 of our stores had only LED lights. The lights of all remaining stores will be replaced in 2022.
Every day Action

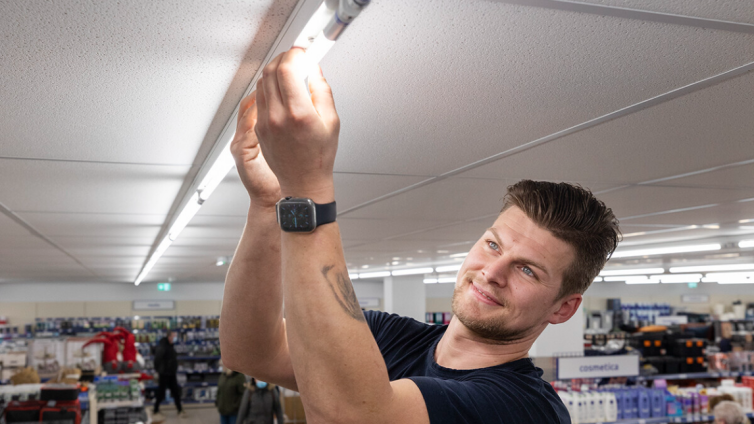